Proper storage and maintenance conditions of inks and pretreatments solutions, in order to ensure consistent quality and performance and therefore extend their shelf-life.
Inks
Handling
The inks used in dtg are water-based pigments, meaning that the color is in the form of solid particles dispersed in a liquid solution that consists mainly from water. Thus, the ink is not a homogeneous solution, but rather a suspension of finely ground particle solids inside a solvent. Although the solid particles may be very small, parameters like time and environmental conditions can cause agglomeration and lead to the formation of larger particles that may clog the nozzles of your printer. In order for the inks to give maximum printing performance, thorough mixing and agitation is required to regain their fully reconstituted formula.
Daily shaking of the printer’s cartridges, preferably at the start of the printing day, for about 1-2 minutes.
Weekly agitation of the inks' containers is also required to maintain this homogenous state. If settling occurred in stored ink and sediment accumulates in the bottom of the container, then agitate the ink for about 5 minutes.
When using an up to 20-liter ink barrel, we recommend using a mechanical roller agitation system, due to the large quantity. If this is not possible, the ink can be agitated using low energy motion by manually rolling the containers on the floor.
Storage guidelines
The ink’s composition is sensitive towards environmental factors. If temperature and humidity levels are not close to the suggested ones, then the consistency of the inks will change. For that reason, the inks should be stored in a clean, dry area with temperature regulated between 10-40 °C (50-104 °F).
Pretreatment Liquids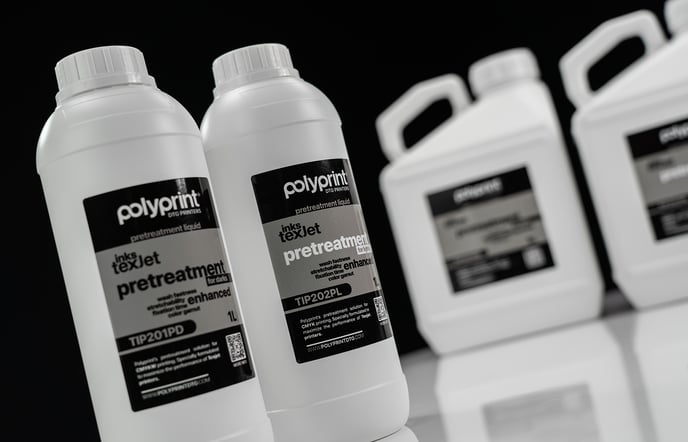
Handling
A pretreatment solution is an aquatic polymeric emulsion. Apart from the polymer that is the main ingredient, it also contains a big amount of salt. Both are ingredients of great density, meaning that can easily precipitate and form sediment. This is why it is important to shake the pretreatment liquids on a regular basis.
Daily shaking of the pretreatment solution, preferably before every use, for about 1-2 minutes.
Weekly agitation of the pretreatment’s containers is also required to maintain its homogenous state. If precipitation occurred in stored pretreatment bottles and sediment starts to pile up in the bottom, then agitate the solution for about 5 minutes.
When using an up to 5-liter pretreatment tank, we recommend using a mechanical roller agitation system due to the large quantity. If this is not possible, the solution can be agitated using low energy motion by manually rolling the containers on the floor.
Storage guidelines
Pretreatment liquids are easily affected by environmental factors such as temperature and humidity. For that reason, all pretreatment solutions should be stored in a clean, dry area with temperature regulated between 10-40 °C (50-104 °F).
Learn here: Inks & Pretreatment Liquids: Fixation times and temperatures